Custom plastic extrusion designed to your industry needs
Custom plastic extrusion designed to your industry needs
Blog Article
Key Advantages and Factors To Consider of Executing Plastic Extrusion in Your Tasks

Comprehending the Essentials of Plastic Extrusion
Plastic extrusion, a staple in the manufacturing market, is a procedure that includes melting raw plastic material and reshaping it into a constant profile. This account, as soon as cooled down, can be reduced into desired lengths or coiled for later usage. The elegance of plastic extrusion exists in its versatility. A wide variety of products, from piping to window frames, can be generated. The process needs an extruder, an intricate maker with a heated barrel, a revolving screw, and a die at the end. The plastic material, in the type of pellets, is fed into the extruder, where it's melted and compelled through the die, taking its form. The choice of plastic and the design of the die identify the product's qualities.
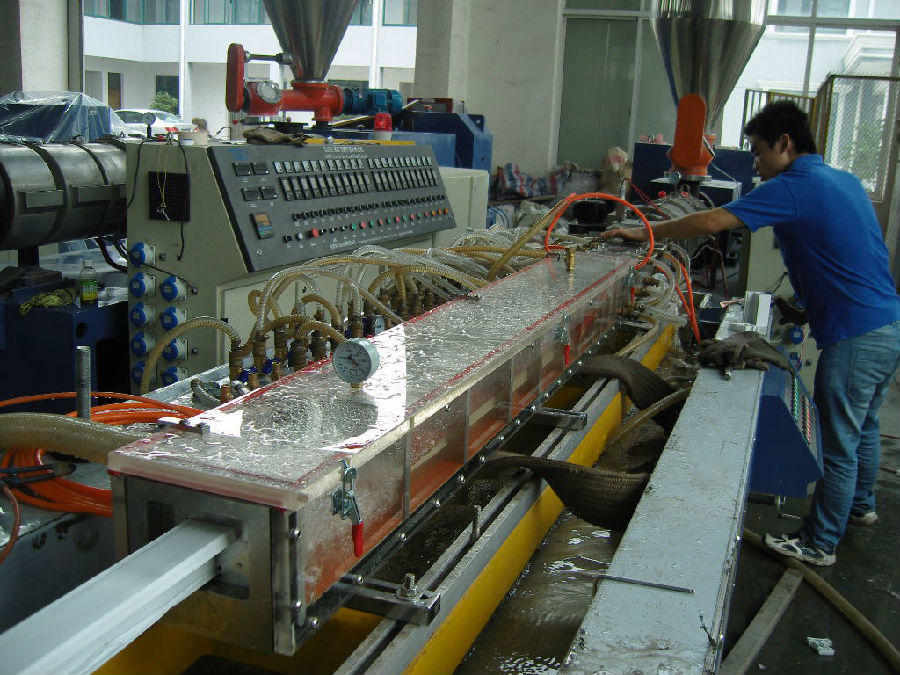
The Economic Benefit of Plastic Extrusion
The economic advantage of plastic extrusion exists predominantly in two areas: affordable material manufacturing and beneficial production speeds. With plastic extrusion, organizations can produce high volumes of material at a reduced price compared to other methods. In addition, the procedure flaunts a remarkable manufacturing speed, substantially decreasing time and more boosting its financial practicality.
Cost-Effective Product Manufacturing
A significant advantage of plastic extrusion is its remarkable cost-effectiveness. This manufacturing process enables for constant, high-volume production with minimal waste, which converts right into reduced costs. The raw products utilized, typically plastic pellets, are reasonably affordable compared to various other materials (plastic extrusion). The process itself needs much less power than numerous other manufacturing techniques, better decreasing costs. Additionally, the extrusion procedure allows for a high degree of accuracy fit the plastic, lowering the need for pricey post-production modifications or adjustments. Additionally, the sturdiness and longevity of extruded plastic products often imply much less need for replacements, adding to lasting cost savings. All these aspects make plastic extrusion an extremely economical choice for several jobs, offering an appealing equilibrium in between price and performance.
Beneficial Manufacturing Speeds
While maintaining the cost-effectiveness of the products, another noteworthy benefit of plastic extrusion exists in its quick production rates. This efficiency in the manufacturing procedure is credited to the continuous nature of the extrusion process, permitting high-volume production in a fairly short time period. The speed of manufacturing directly associates to a reduction in labor costs and an increase in output, thus boosting the overall financial viability of the procedure. Furthermore, the fast-paced manufacturing does not compromise the top quality of the last product, ensuring consistent and dependable results. This combination of speed, quality, and cost-effectiveness underscores the substantial economic advantage of carrying out plastic extrusion in numerous projects.
Convenience and Modification: The Strengths of Plastic Extrusion
Among the popular toughness of plastic extrusion lies in its adaptability and modification possibility. These top qualities unlock to unlimited style possibilities, offering manufacturers the capability to customize items to particular demands. like this This heightened level of modification not just improves product capability however also dramatically increases product originality.
Unlimited Layout Possibilities
Plastic extrusion radiates in its capability to supply almost see endless layout opportunities. Plastic extrusion can manage a variety of plastic kinds, broadening its application range. With plastic extrusion, the layout possibilities are basically endless.
Enhancing Product Uniqueness
The convenience of plastic extrusion can significantly improve item uniqueness. This process allows designers to experiment with various forms, sizes, and shades, providing them the liberty to produce distinct items that stand out in the market. It is this customization that provides a distinct identity to each item, distinguishing it from its rivals.
In enhancement to its visual benefits, the customizability of plastic extrusion also provides functional benefits. Designers can modify the properties of the plastic according to the details requirements of the application, boosting the item's functionality. They can make the plastic more adaptable, a lot more durable, or much more resistant to heat, depending on what the item requires. Hence, plastic extrusion not just increases product individuality however additionally its utility and marketability.
Style Limitations in Plastic Extrusion: What You Need to Know
Just how can design limitations possibly impact the procedure of plastic extrusion? While plastic extrusion is versatile, style constraints can curtail why not look here its benefits. Certain complicated designs may not be feasible due to the restrictions of the extrusion procedure, potentially restricting the creation of complex profiles. The process is much less appropriate for hollow or multi-chambered structures. Additionally, the extrusion procedure may not constantly supply the wanted surface area finish, particularly for those requiring high gloss or optical quality. Product selection can also present difficulties, as not all polymers appropriate for extrusion. High-temperature immune plastics, for example, may present problems. Recognizing these restrictions is essential for reliable application of plastic extrusion in your jobs. plastic extrusion.
Reviewing the Ecological Impact of Plastic Extrusion
While understanding design constraints is a significant aspect of plastic extrusion, it is just as important to consider its environmental ramifications. The process of plastic extrusion involves melting plastic materials, potentially launching unsafe gases into the environment. Using recycled plastic products in the extrusion process can minimize environmental impact.
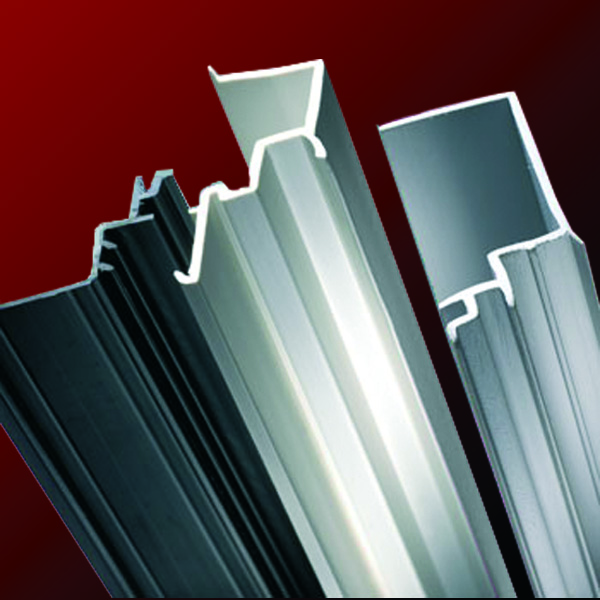
Study: Effective Projects Making Use Of Plastic Extrusion
Success tales in the field of plastic extrusion abound, demonstrating both the flexibility and efficiency of this manufacturing process. plastic extrusion. Another successful instance is the manufacturing of plastic movie for packaging and farming. These circumstances show plastic extrusion's critical duty in numerous fields, attesting to its versatility, cost-effectiveness, and reliable output.
Final thought
In verdict, plastic extrusion offers a efficient and affordable approach for producing complicated shapes with marginal waste. Integrating plastic extrusion right into tasks can lead to effective outcomes, as evidenced by numerous situation research studies.
Plastic extrusion, a staple in the manufacturing industry, is a procedure that includes melting raw plastic material and improving it into a continuous profile. Plastic extrusion can handle a range of plastic types, broadening its application range.How can create limitations potentially influence the procedure of plastic extrusion? The process of plastic extrusion involves melting plastic materials, potentially releasing dangerous gases into the environment. Utilizing recycled plastic products in the extrusion process can decrease environmental impact.
Report this page